Structural Design of Glass-to-Metal Sealing
Nathaniel Horton, Ph.D. & Eric Skaar Ph.D.
The Issue
Structural designs of the modern era will be driven by the ability to maximize strength mechanically and performance electrically while minimizing the volumetric footprint of an assembly.
Exploring Glass-to-Metal Sealing Opportunities
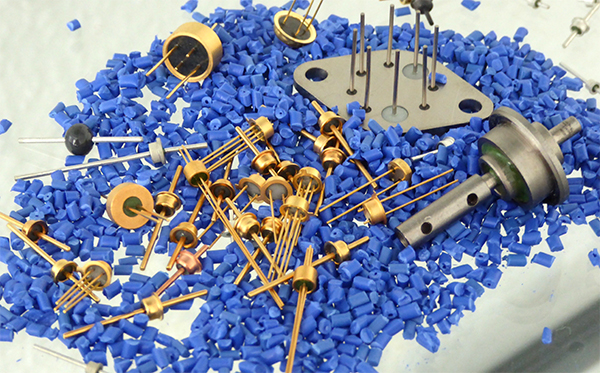
Glass-to-metal (G/M) sealing can be described as an art-form based in science; meaning much of what is in practice is based on libraries of empirical data, but modern designs are now relying on analytical science. Being so, when considering any new application a thorough investigation of available commercial assemblies is prudent: some existing qualified designs are often easily modified slightly to fit integration. Alternatively, when a new design is required it may be possible to use a simpler design of an intricate seal to serve the intended purpose.
A potential first step in the acquisition/design process is to identify what functional category to which the seal conforms, then researching existing marketplace designs. Several broad categories encompass: electrical feedthroughs; hermetic connectors; lamps, lasers and sight glasses; sensors, switches, relays, and transducers; electronic packaging; batteries; fuel cells; telecommunications and semiconductors; high pressure initiators/actuators/detonators; biomedical implants; cryogenics or high temperature detectors.
The next step in the procurement process is turning to engineering criteria: two pins, three pins, square or coaxial header, hermetic package, and so on. This phase identifies the mechanical, electrical, hermetic, thermal, and other specific performance criteria the assembly will be required to achieve over its entire serviceable lifetime. To assist in this step, study the Glass-to-Metal Matched Seals Versus Unmatched Seals Guide, and select the appropriate design based on the defined specifications.
The final step should be acquisition cost and production feasibility studies. Consider: complex designs become intricate for glass to metal seal manufacturers, and incur substantial production cost. It is not uncommon for production cost to be up to 10 times that of simple designs. Thus, it is important the end user’s design engineer(s) and the sealing engineer both analyze the assembly design from an end use performance continuum and a manufacturability perspective. Afterall the most elaborate seal design, while functionally superior may be unimaginably expensive and prohibitive to produce.
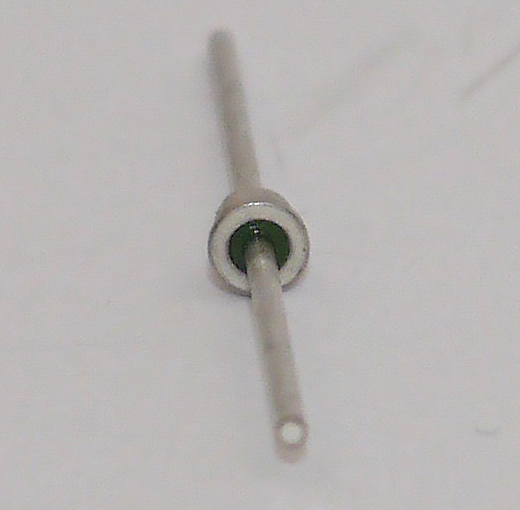
Glass-to-metal seals have now been in use for over a hundred years, starting with the early Houskeeper or vacuum tube seals, and advancing to elaborate SOFC fuel cells, and beyond. It is now recognized there are many factors to the quality of a seal, from pre-cleaning and pre-oxidation, to furnace atmosphere, and presence of carbide precipitates. Science will guide mastery of these production factors and moreover the development of new advanced sealing media to push the design envelope into the foreseeable future and ensure G/M seals are ever relevant. Glass-Ceramic-to-metal seals are a more recent such development that offer unique properties to potentially diversify applications. From the simplest coaxial feedthrough to the most elaborate miniaturized biomedical implant, understanding and developing the correct design methodology can maximize the end result.
Ceramic Seals
Ceramics are a separate sealing medium outside glass-to-metal and are omitted from this write-up, nonetheless they deserve a brief mention.
Predominately, ceramics have a higher melting temperature than metals and do not bond/wet directly, and therefore fusion processes cannot be employed. Most often ceramic seals are manufactured with an additional processing step to either indirectly metallize the bonding surface or directly apply a braze or solder alloy to the interface.
Because of their high temperature performance ceramics also play a role as a structural support; in some cases ceramic preforms are inserted between glass seals and not flowed to maintain geometric offsets.
As the sealing medium, seals are designed near to matching to prevent plastic deformation of the brazement. Ceramic seals offer excellent strength and high temperature resistance–provided the braze/solder is not exceeded–but can not be flowed to fit complex geometries.
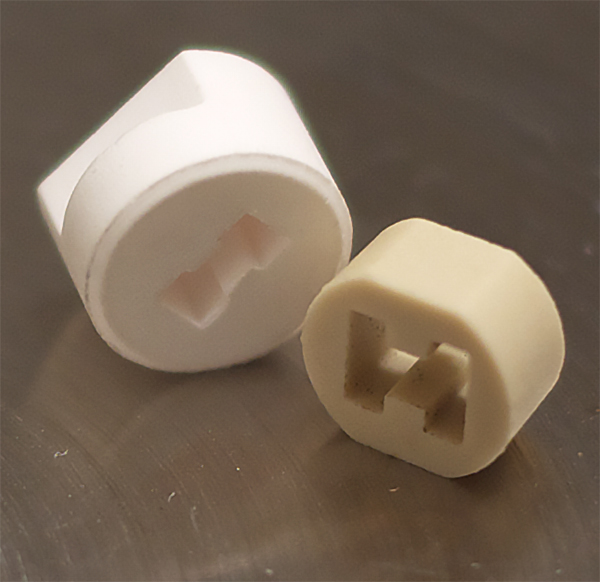
For a sample of commonly used ceramic materials that fit these criteria, please review our Alumina ceramic and Steatite ceramic compositions.